ES Process PET Bottle Washing Line
Efficient and Smart - PET Bottle Recycling Solution
Background
With a highly developed economy but increasingly scarce resources, high automation, less labor, low energy consumption, and high equipment efficiency are necessary for developing the PET bottle recycling industry. Higher market demand has been put forward regarding equipment occupation, unit energy consumption, safe operation, stable operation, durable equipment, and rPET flakes quality. BoReTech brings up a high-efficiency module design for particular waste PET bottles, which simplifies the process, reduces investment and production costs, and raises the PET recycling process to another level. This is BoReTech's fifth generation recycling process——ES process PET bottle washing system.
Product Feature
Relying on market demand, the ES-PET bottle recycling process adopts an integrated process layout to reduce equipment footprint, improve equipment automation, optimize operation safety, make the machine more durable, operate more stably, and decrease the number of devices, making the energy consumption per ton flakes produced is much lower than the typical PET bottle recycling process. However, the quality of the final PET flakes is no different from that of the flakes produced by the typical process which is stable and can be drictly used in the production of food contact bottle to bottle and Micro denier fiber.
BoReTech adopts integrated equipment technology to reduce area occupation and improve equipment automation is a major feature of ES process PET bottle recycling system. De-labeling combined with bottle pre-washing sections. The two functions are integrated into one module, which reduces the floor space by more than 25% and reduces the unit energy consumption by nearly 13%. The washing performance and label removal rate are very efficient.
Compared with the standard PET bottle recycling process, this module has soaking and powerful washing functions. Unity and renewing of temperature and chemical concentration for batch flake washing. Modular design, prefab pipeline, standardization of parts, and precise connection save the installation time. Special ultrafine filtration system can separate tiny particles bigger than 5μm. Maintaining the concentration and cleanliness of chemical process water, extending the lifetime, and saving detergent consumption. It is in line with the development concept of green environmental protection and resource regeneration.
Enhanced rinsing module separates most of the contaminants. The high-performance ultrasonic washing machine is used to impact and peel off the dirt on the surface of flakes to achieve high-performance cleaning. It can thoroughly remove the remaining detergent on the surface of flakes. rPET flakes quality can meet the production requirement of the Ultrafine-denier filament, and the filtration performance in the extrusion process improves by 25%. The precision filtration system prevents the PET flakes from being polluted by contaminants in washing process water. Enhanced rinsing machine has stronger washing and flushing performance, the residual impurities and lye on the surface of the flakes are separated. It has been provened that mixed flakes overflow under high-speed stirring, quickly eliminating the liquid and recycling so that the rinse water is clearer.
Highlights
1. Small Area Requirement: The ES process PET bottle washing line is more compact and integrated. The land area requirment reduces by 25%, compared with the typical washing process. save land and other costs.
2. Highly Modularized: Achieve compact combination and integration among equipment function and process design into a multi-functional module.
3. High-Quality rPET Flakes: The flake quality is more reliable than the typical process, and the filtration performance in the extrusion process improves by 25%. The flakes can be directly used in the production of bottle-to-bottle and Micro-denier filament. The physical and chemical properties of recycled PET pellets are close to virgin pellets;
4. Low Production Cost: With the assistance of a high-automation system, the manpower requirement is much lower than that before. The production efficiency gets higher, and the unit utility consumption gets lower.
5. Convenient Maintenance: Due to the standardization and modularization of the ES process equipment, the spare parts and the maintenance work are much simpler and easier. The malfunction rate is much lower than that before.
6. Environmental Protection and Sustainability: The chemical washing water in-line filtration system can minimize the consumption of water and detergent.
Input Capacity
3000/6000 kg/h
Key Technology for PET Bottle Recycling
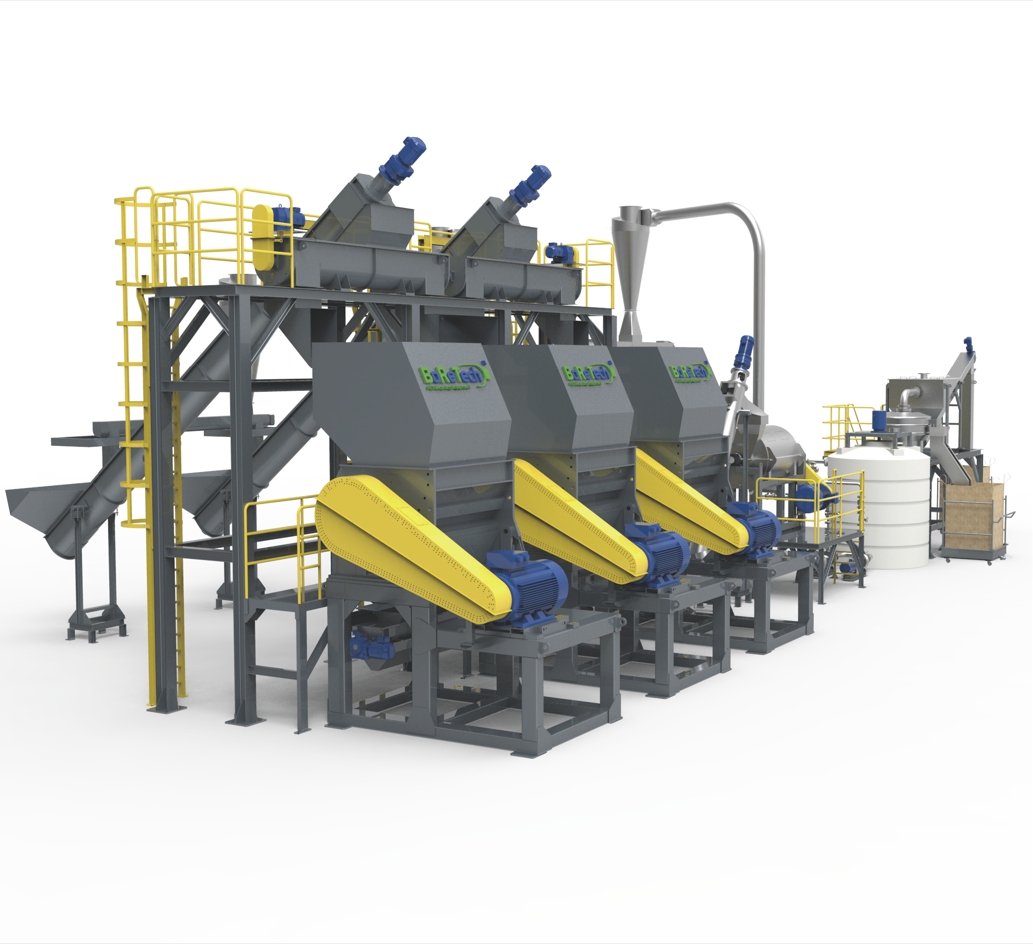
Crush and Drying Module
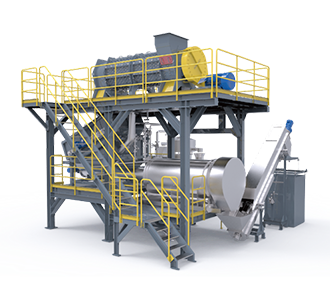
Label Removal and Flushing Module
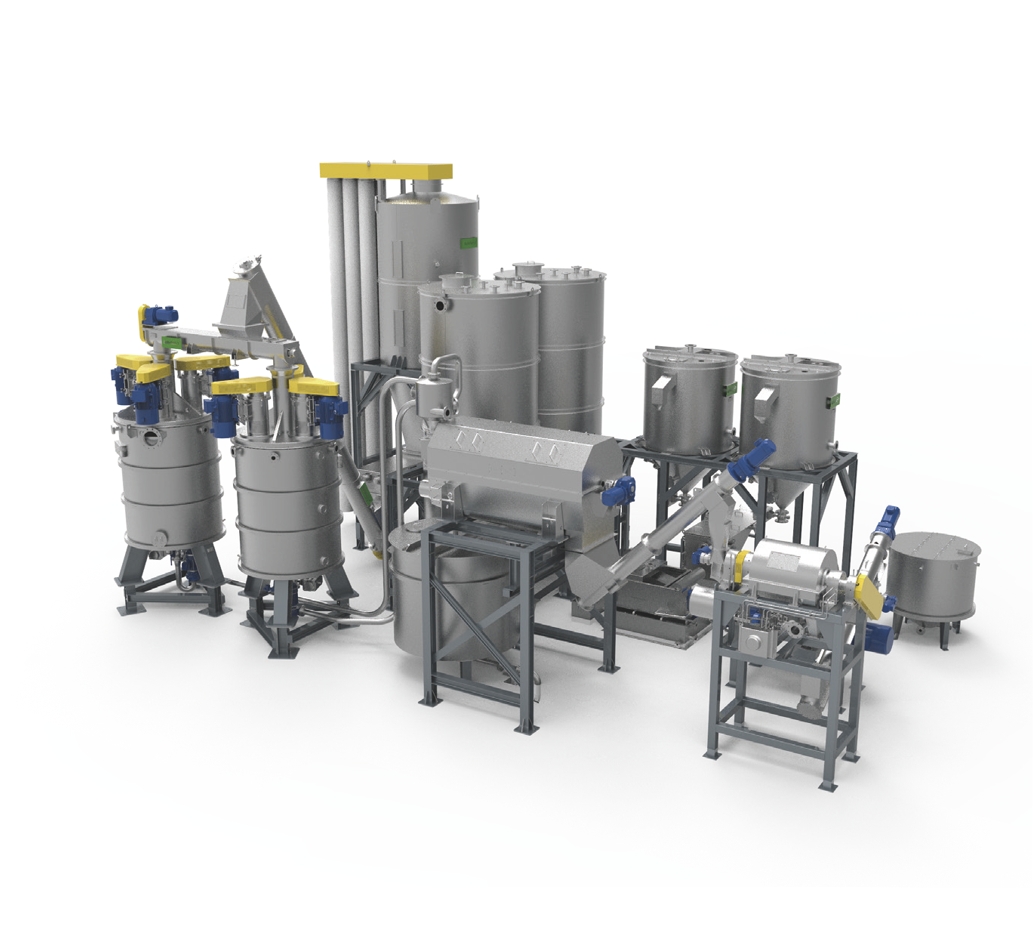
Intensive Hot Washing Module
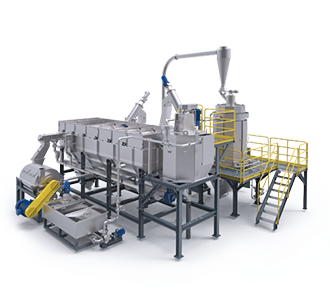
Enhanced Rinsing Module
3D Layout
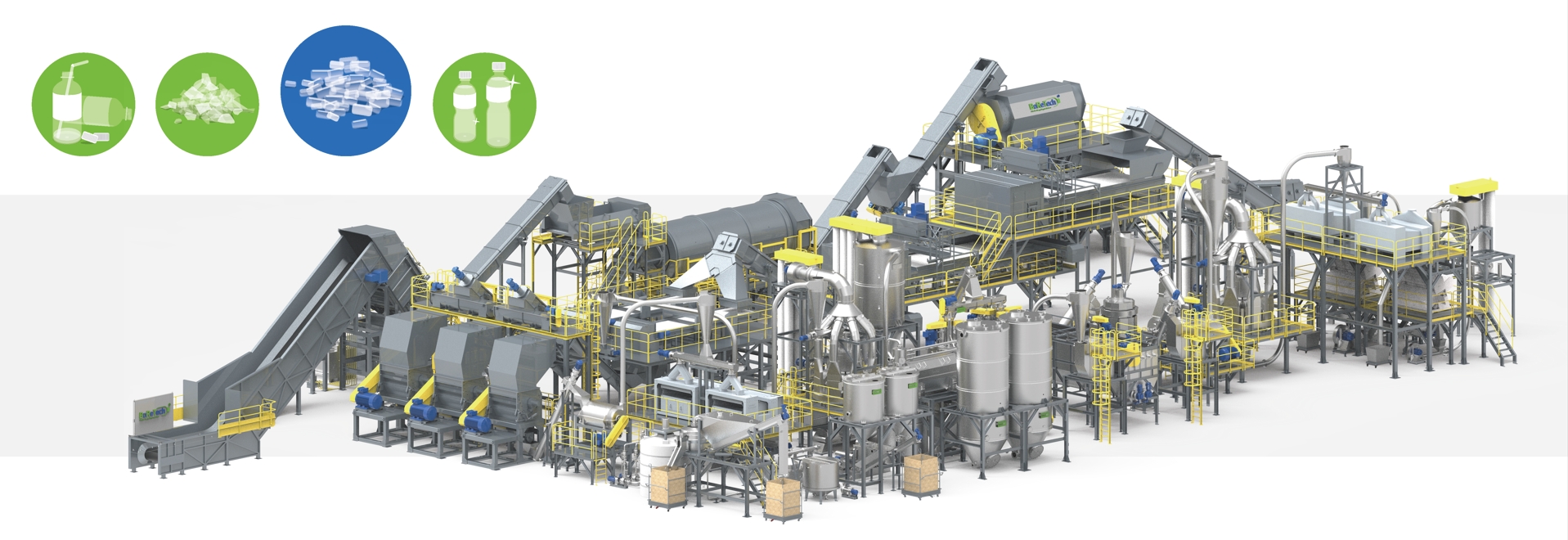
ES PROCESS for PET Bottle Recycling
Ps. A standard sampling of the food-grade PET bottle recycling process, equipment configuration and the process will be optimized according to raw materials