Where's the quality assurance of recycled PET come from?
2022-08-23
The total consumption of global PET bottles is 22,343 kt, of which 11,370 kt is recycled (according to Wood Mackenzie Chemicals 2020 report). Generally, the average global recycling rate of waste plastics is still low. With the international brands announcing an increase in the use amount of recycled plastics, the global commitment added a mandatory virgin plastic reduction target in 2021. More than 60 brand owners and retailers have set corresponding virgin plastics volume reduction targets. The new agreement calls for a drop in absolute use of virgin plastic by nearly 20% by 2025 compared to 2018. Reduction in plastic usage is a good trend, but it is not enough to immediately solve the long-standing plastic pollution problem. In the long run, recycled plastics gradually replace virgin plastics, promote waste plastic recycling, and sustainable economic development is the focus of plastic packaging and application development.
PET plastic recycling mainly comes from post-consumer PET bottles. More than 95% of PET plastic recycling worldwide is achieved through physical recycling. Chemical recycling methods have not been widely used and commercialized due to high investment costs, high production costs, and complex processes. However, whether it is recycled by physical or chemical, de-labeling, label removal, crushing, and PET flake washing are all necessary processes in advance.
The amount of recycled PET is increasing and trending to a higher grade by global brands. The PET bottle balers' composition and downstream applications influence the PET bottle recycling configuration. BoReTech has been in the PET bottle recycling industry for more than 30 years and has rich practical experience in PET bottle washing and cleaning.
The advantages of the BoReTech PET bottle recycling process
- Customized washing process, propose different modular recycling processes for different countries and regions;
- Large processing capacity, the input capacity from 3000 to 9000 kg/h;
- In-line water-saving system, only one cubic meter of industrial water is consumed per ton of flakes output;
- Inline sub-product collection system, saving labor input;
- Modular design solutions;
Main Modular Introduction
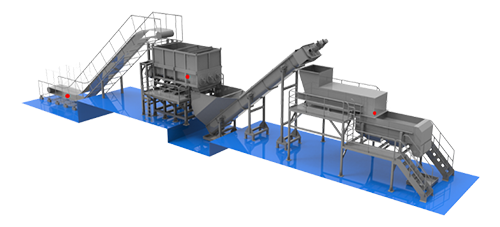
- The PET bottle bales are broken up through the de-baling device.
- Separate impurities through the metal removal device by multiple steps.
- Quick disassembly design.
- High label separation and low bottle broken rate.
- Large input capacity, the long service life of blades.
- Label Blower.
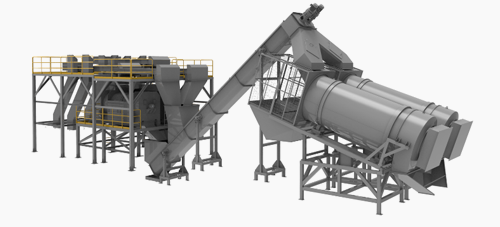
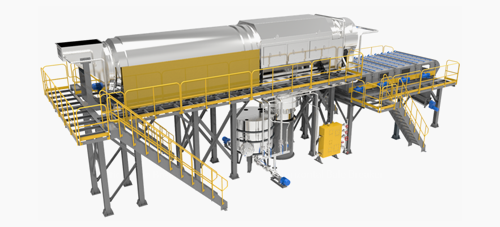
- High-temperature washing+ Chemical washing.
- Spraying washing to remove impurities.
- Bottles return to original form after pre-washing.
- Separate paper label, PP label, caps, rings, and glues.
- Inline Chemical water circulation system.
- Wet crushing makes fewer PET fines.
- Crushing bottles to flakes in an indicated size.
- Prolong crusher blades service life.
- Remove impurities from PET bottles.
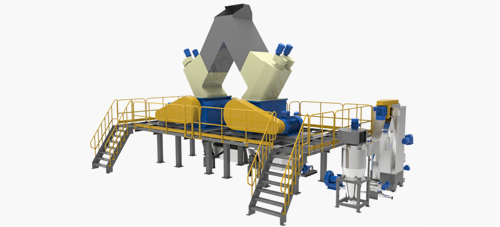
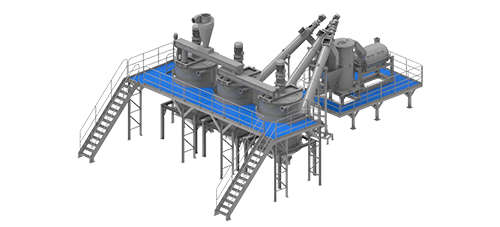
- Chemical water circulation system.
- Remove glues and adhesive with chemical water.
- Combine high-Temperature washing, mechanical friction force, and caustic soda.
- Separate gules, paper, and fiber impurities to guarantee high-quality PET flakes.
- PH value of PET flakes meets food grade.
- Residual chemicals and fines.
- Rinsing water inline processing.
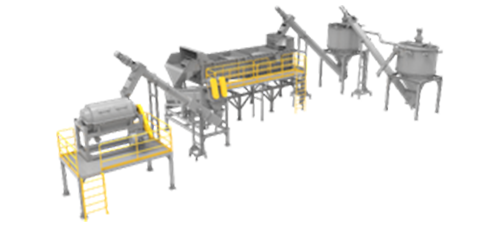
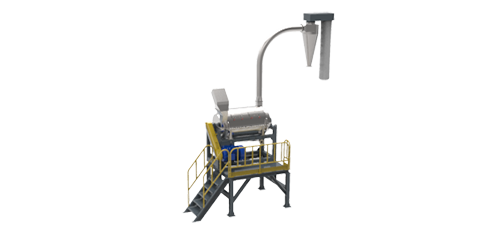
- Flakes moisture reduced below 0.7%.
- Some flakes will be crystallized.
- Provide conditions for extrusion.
- Separate PS, PA, PET, and PVC film from PET flakes.
- Reduce small-size PET flakes, PET fines, and small impurities
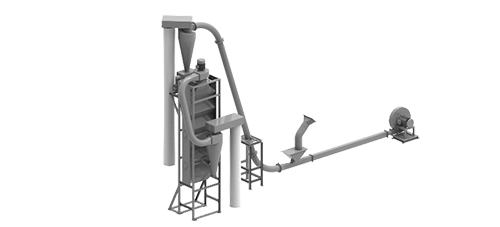
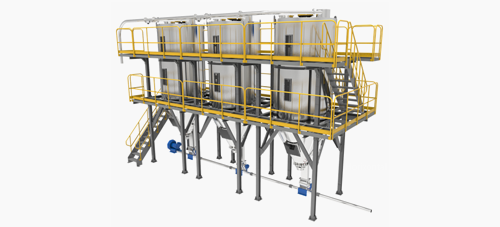
- Guarantee PET flakes quality index in a stable range.
- Inline quality analysis.
- Classify PET flakes according to the sampling inspection result.
- 3A Level quality flakes.
- Sub-Product Collection System.
- Special designed shaking system.
- Inline weighing device.
- Maximize bulk density.
- Reduce packing and transportation cost.
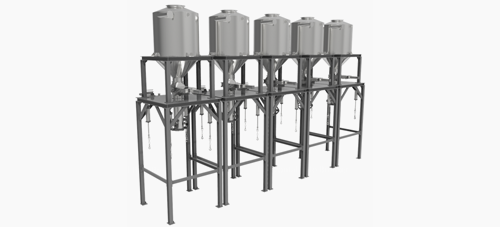